V-Cone® for LNG: Safety and Quality Benefits in Cryogenic Processes
The V-Cone is often implemented in upstream, midstream, and even downstream oil and gas processes to measure a variety of flow media in various states and temperatures. The V-Cone’s options for customization are among the many factors that prompt customers to choose this meter for such diverse and varied applications. Additionally, it’s often the quality measures behind McCrometer’s engineering and manufacturing teams that ultimately get the V-Cone specified into projects such as liquified natural gas (LNG) and other cryogenic applications.
Let’s review.
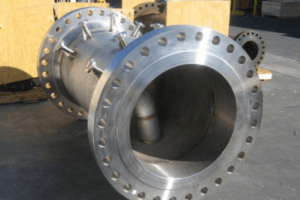
A V-Cone customized with multiple taps.
Cryogenic for LNG
In the LNG process, gas is extracted from the earth, liquified, shipped off, received by regassification plants to be reconstituted, and finally sent to the consumer. Liquifying the natural gas also reduces its volume, creating a cheaper storage and transport process, as liquifying the gas allows operators to reduce their volume 600:1. Furthermore, in their gaseous state, hydrocarbons are volatile, and cryogenic liquefication such a hazardous material ultimately reduces the risk factor, as at below -328.8 degrees Fahrenheit (-161 degrees Celsius) LNG is non-flammable.
Many major LNG projects who have implemented liquefaction processes have used V-Cones for flow measurement. This process, among others, prioritizes plant performance and economic efficiency. Liquefaction processes are insulated, complex systems that require metering solutions that are durable and consistent. As one of many variables in that system, the V-Cone is relied upon for its minimal-to-no maintenance needed and 25+ year life expectancy.
Non-LNG Cryogenic Applications
Cryogenic applications exceed the LNG market – in fact, McCrometer has provided V-Cones for very specialized, unique cryogenic projects since entering the market in 1985. The V-Cone was selected to measure cryogenic coolant for detectors on a satellite in outer space, due to the meter’s ability to measure flow media extremely close to absolute zero. The V-Cone’s lifespan and durability were extremely beneficial as well – we can’t think of an installation where ongoing maintenance would be more inconvenient!
The V-Cone as an Emergency Shutdown System Instrument
Other cryogenic applications, such as gas compressor discharge flow, rely on the V-Cone for its customization flexibility. In addition to the V-Cone’s range of standard and exotic materials for manufacturing, multiple taps can be engineered into the final product as well. Beyond the normal process control taps, additional taps for checks and balances add a level of redundancy to bolster customers’ emergency shutdown systems (ESD). The V-Cone can be customized with multiple taps as a part of a Safety Instrumented System (SIS) to provide measurement redundancy to meet the required Safety Integrity Level (SIL). For cryogenic processes, V-Cone taps can be manufactured with different standoff heights to accommodate thermal and acoustic insulation.
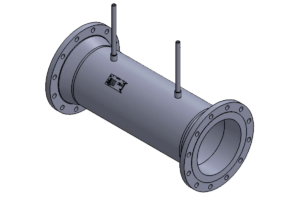
Taller standoff heights on a V-Cone to accommodate insulation.
Additional V-Cone Specifications for Cryogenic Applications
Other popular specifications for these applications include 304L stainless-steel construction due to the characteristic low temperature of cryogenic flow media. Plenty of other materials are available such as nickel-based alloys and even zirconium if required. McCrometer’s engineers work on cryogenic projects often requesting low temperatures of -320 degrees Fahrenheit (-195 degrees Celsius) prompting our teams to perform more stringent quality checks and non-destructive testing (NDT) related specifically to temperature.
Ensuring the integrity of the welds at extremely low temperatures is critical. V-Cones for cryogenic processes are manufactured with different weld procedures to accommodate cryogenic flow media and avoid brittle fracture. NDTs are often performed on the raw material as well as the manufactured flow meter, and may include impact testing, radiography testing, and penetrant testing, often chosen to detect fatigue cracks. All of these NDTs verify the sustainability of the welds and authenticate that in-house best practices were followed.
Unique Project? No Problem.
Each cryogenic flow project will face different and unique specifications and environmental factors, and each customer will have their own project goals that McCrometer can help them achieve. Custom V-Cones are manufactured to the specifications laid out by the customer and/or their engineering firm. We encourage our customers to communicate with our engineers early on in their design process; each customer is an expert in their project, and our engineers are experts in flow measurement. McCrometer prioritizes collaborating with our customers and channel partners on their challenging flow projects to help develop and manufacture lasting metering solutions.
For more information on the V-Cone and our entire oil and gas suite of products, visit www.mccrometer.com or contact the factory by emailing quotes@mccrometer.com for a quote on your next flow project.
Related Posts
Featured Posts
Small Package, Big Impact: The Importance of Desiccant Cartridge Maintenance
You’ve likely seen a desiccant cartridge, in the form of the small silica gel packet accompanying food products, or the activated carbon packet at the top of pharmaceutical bottles. It’s also commonly used in electronics and near sensors, especially for...
Choosing the Right Non-Contact Flow Meters: A Quick Dive into Radar and Laser Technologies
When measuring open channel flow wastewater and stormwater, non-contact flow technology is the ideal method, able to provide an accurate velocity and flow rate. Especially in the wet weather season, non-contact flow technology greatly benefits open channel...
Meeting BABA Compliance and Expanding Opportunities
Content Recorded and Published at WEFTEC in October 2024 In this episode of The Water Online Show: On Location, (now former) McCrometer President Pete Oveson dives into the company's story and recent developments shaping its future. He begins with an overview of...
Request More Information