Non-Destructive Tests: What Is It, and Do You Need One?
While there are many quality control procedures McCrometer performs to ensure a meter is manufactured to spec and in accordance with ISO 9001 (among other standards), there’s a specific test that some McCrometer customers opt to have performed on their meter. Known as a non-destructive test (NDT), it’s the process of inspecting and testing a meter to ensure it is fit for use without damaging the finished product.
So, what methods of NDTs are available, and should you opt to have one performed on your flow meter? We spoke with the welding and sustaining engineers at McCrometer to get the expert advice.
The Basics of NDTs
Historically performed on metal materials, NDTs can be performed on electromagnetic (mag) meters, but it’s more commonly requested for our V-Cone line of meters. There are multiple NDTs that can verify the strength of welds and integrity of the meter, one of which is a radiography NDT.
A radiography test (RT) is based on the same principle as an x-ray when performed on a bone; either gamma rays or x-rays are used to determine if there are any flaws in the weld or any of the metal materials, like an air pocket. An RT compares density in the material; however, depending on the code of construction there is an acceptable level of faultiness, as all materials contain some level of imperfection. This test is typically performed on butt welds on flanged meters.
Ultrasonic testing (UT) looks for variance of thickness or discontinuity in the meter by running a probe or transducer across the surface of the meter to find flaws, air pockets, or any difference of material that might cause problems in the future. This method of testing is highly accurate and can penetrate deep welds, a major benefit for thick-walled meters or meters of a large nominal pipe size.
Penetrant testing (PT) is a surface test that utilizes a dye sprayed on the metal surface that will seep into any cracks or flaws in the material after a period of dwell time. Once cleaned off, a visual inspection will determine if any bleeding of the dye occurred, indicating a flaw in the material. This is a very cost-effective NDT and is often the test of choice to detect fatigue cracks or other in-service issues in meters during technical support troubleshooting. This is typically used for fillet welds as other typical NDT methods (RT/UT) can sometimes be troublesome to review on fillet or branch connections.
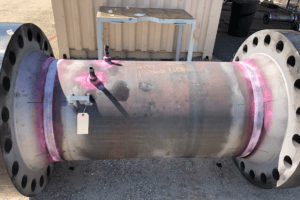
A V-Cone in the “dwell” stage of penetrant testing.
The most basic of the NDT is the visual test (VT), where a quality inspection is performed on the meter, visually searching for any dents in material or flaws in the weld. This is the most common test performed, as it’s cost-effective and requires little equipment.
When to Select an NDT
Each of the above methods of NDTs are frequently chosen to be performed by the customer or their engineering, procurement, and construction firm (EPC). Depending upon the application, such as a highly combustible flow media or high-pressure application, a McCrometer engineer may recommend an NDT for quality assurance purposes.
More often than not, NDTs are performed on our V-Cone product line, but we have also had NDTs performed on our mag meters as well. An NDT can be performed on any of our metals-based products in order to verify the suitability of the welds and authenticate that in-house production best practices were followed.
NDTs for Peace of Mind
An NDT offers quality assurance and peace of mind to customers; choosing an NDT is a risk assessment. In applications flowing low-pressure water, there is a lower level of risk if there is a faulty weld, and the customer might not opt to spend the money and time on an NDT. However, if there is a flaw in the manufacturing of a meter in an oil and gas application, that customer has a higher level of risk, especially if there is an accelerant nearby and the pipeline is flowing a flammable media. That’s the purpose of an NDT – to ensure customer confidence in the meter and to minimize levels of risk for the flow project.
When deciding to have an NDT performed on a meter, consider the application and decide the worth of having peace of mind. For many McCrometer customers who have stringent specifications for their meters, in oil and gas, municipal, and industrial markets, an NDT is money well spent. It provides documentation for the customer and is simply another method of ensuring quality on a meter investment.
NDTs on Your McCrometer Meter
The McCrometer engineers almost always recommend an NDT performed on our V-Cones; providing customers with quality assurance and confidence in their metering is a priority. While we offer the NDTs we talked about above, that’s not the extent of the NDTs we can perform on your meter. Depending upon customer specs, we can meet custom NDT requirements upon request.
To learn more about non-destructive testing on McCrometer meters, reach out to the factory. If you’re ready to include an NDT in your meter order, request a quote.
Related Posts
Featured Posts
Small Package, Big Impact: The Importance of Desiccant Cartridge Maintenance
You’ve likely seen a desiccant cartridge, in the form of the small silica gel packet accompanying food products, or the activated carbon packet at the top of pharmaceutical bottles. It’s also commonly used in electronics and near sensors, especially for...
Choosing the Right Non-Contact Flow Meters: A Quick Dive into Radar and Laser Technologies
When measuring open channel flow wastewater and stormwater, non-contact flow technology is the ideal method, able to provide an accurate velocity and flow rate. Especially in the wet weather season, non-contact flow technology greatly benefits open channel...
Meeting BABA Compliance and Expanding Opportunities
Content Recorded and Published at WEFTEC in October 2024 In this episode of The Water Online Show: On Location, (now former) McCrometer President Pete Oveson dives into the company's story and recent developments shaping its future. He begins with an overview of...
Request More Information