Dewatering Flow Measurement: Considerations in Meter Selection
What is dewatering?
Dewatering is any removal of water from a pit, underground utility, foundation, or substructure, and can be found in industries like mining, mineral processing, municipal wastewater, and construction. It’s often done to improve the ground quality, especially in locations where the water table is high and the area has surrounding water sources such as ponds, lakes, or rivers.
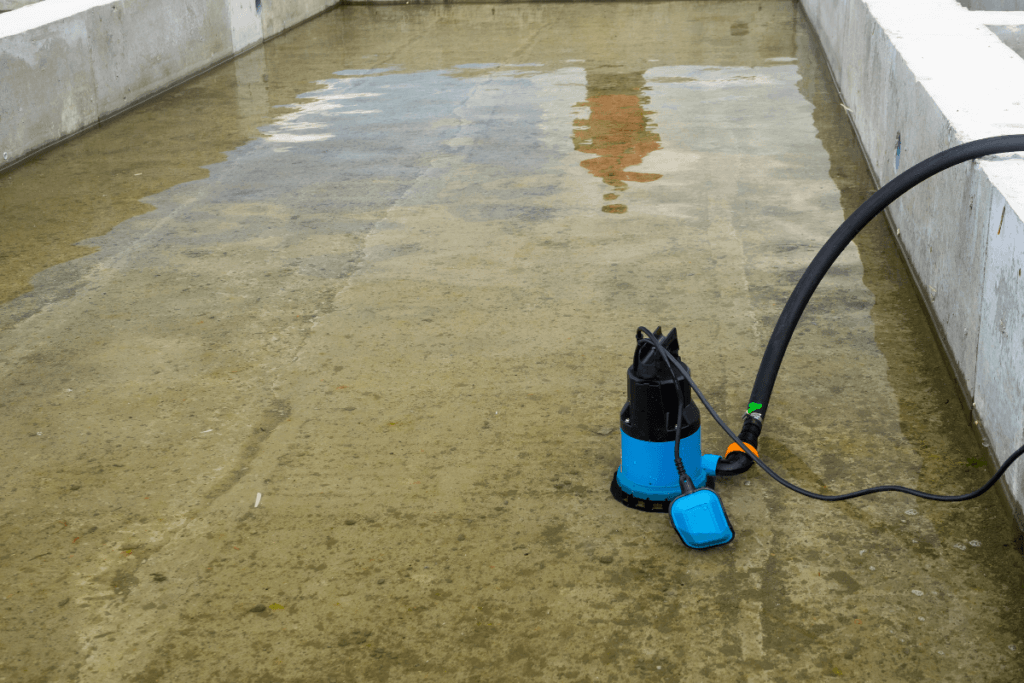
Dewatering at a construction site.
Dewatering can involve surface pumping, such as dewatering ditches or ponds during a construction excavation process, and deep well drainage, which is removal of groundwater through use of wellpoints and vacuums. Additional methods such as flood control dewatering, tunnelling, and bypass are all utilized in mining, construction, and wastewater industries.
Why is dewatering critical for these industries?
Certain businesses and verticals engage in dewatering due to the inconvenience of water. For instance, rainfall can cause flooding in pits and mines, which will need to be dewatered in order to resume operation. Businesses such as fuel depots need to remediate water immediately to avoid contamination. The mining industry is similar in this regard, needing to discharge rainwater and runoff and treat for possible contamination per local and state regulations.
What are the challenges of metering in a dewatering application?
Depending upon the industry and dewatering location, the challenges may vary.
- Duration of dewatering operations. Dewatering can be a semi-permanent application, due to shifting operations in construction and mining. Operators need something easy to install, maintain, and get the flow data back up and running for the next operation.
- Dewatering applications often deal with suspended solids in the flow media, which could be rocks, gravel, silt, and other corrosive material that could damage meter components or skew readings. Engineers and operators require a rugged meter that can withstand the dewatering flow media as well as the periodic removal, transportation, and installation at various dewatering sites.
- Data accessibility. Getting flow data can be a challenge for operators, as remote dewatering installation sites often lack reliable power supply and have precarious access points for manual meter reading. Telemetry may be an option for data accessibility, but a datalogger would also be a benefit, especially to users needing to report flow to regulatory organizations.
- Vibrational resonance. Surrounding equipment such as hydraulic pumps and borehole pumps can cause significant noise interfering with the accurate measurement of some flow meters, becoming a challenge for operators.
Propeller Meters for Dewatering Applications
While certain mechanical meters like turbines and paddle meter may not hold up against suspended solids and silty water, propeller meters such as McCrometer’s Mc®Propeller rise to the challenge. The stainless-steel bearings aren’t affected by the debris in the flow, and the electronics are protected from water intrusion. Offered with a mechanical register, digital FlowCom, and the telemetry unit FlowConnect™, the McPropeller is an economical choice for engineers and operators wanting a workhorse meter with minimal features.
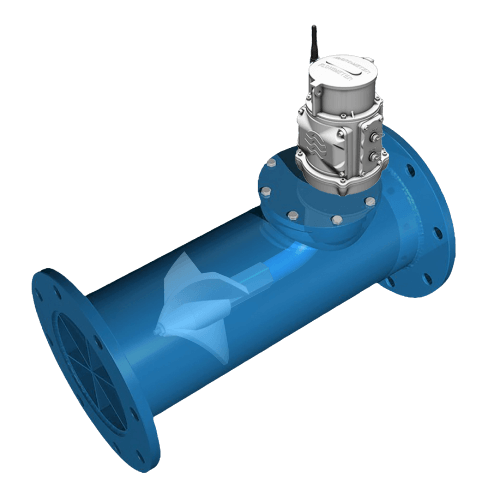
The MW500 configuration of the McPropeller.
The recommended configurations are the MW500 series McPropeller, which provides a top-plate propeller bolted into a flanged flow tube, easily installed into an existing pipeline and minimally maintained. The ML series McPropeller is the drop-in assembled for customers who already have the existing pipe, or who need to purchase a replacement. The McPropeller performs well in dewatering applications measuring silty or debris-filled flow media that’s ambient temperature, low pressure, and with minor head pressure to overcome if installed deep in a mine or shaft.
Mag Meters for Dewatering Flow Measurement
For semi-permanent or permanent dewatering applications, the Dura Mag™ is a good fit, especially when the installation site is nearby a pump. The Dura Mag is an extremely robust option for slurries and sludge dewatering as there are no moving parts or intrusions in the line. Instead of a traditional rubber line, the Dura Mag features the UltraLiner™, a fusion-bonded epoxy that contributes to the mag’s rugged performance. The UltraLiner has a lifetime guarantee against delamination and tearing that might get sucked into a pump and cause expensive equipment damage. The Dura Mag is durable, easy to install, and simple to maintain.
A mag meter is also a better flow option for operators and engineers needing more functionality than a propeller meter, such as a datalogger, battery power, or remote electronics mounting.
Choosing a Flow Meter for Dewatering
When deciding which meter fits your flow application best, consider these questions:
- What is the goal of flow measurement?
- Do the meter’s specifications and features help meet those goals and overcome the application’s challenges?
- Does the meter fit the initial project budget or provide a worthwhile return on initial investment over the life of the product?
- Is the meter easily integrated into the overall operation?
For additional questions and information, consult your local McCrometer authorized representative, or contact the factory directly.
Related Posts
Featured Posts
Small Package, Big Impact: The Importance of Desiccant Cartridge Maintenance
You’ve likely seen a desiccant cartridge, in the form of the small silica gel packet accompanying food products, or the activated carbon packet at the top of pharmaceutical bottles. It’s also commonly used in electronics and near sensors, especially for...
Choosing the Right Non-Contact Flow Meters: A Quick Dive into Radar and Laser Technologies
When measuring open channel flow wastewater and stormwater, non-contact flow technology is the ideal method, able to provide an accurate velocity and flow rate. Especially in the wet weather season, non-contact flow technology greatly benefits open channel...
Meeting BABA Compliance And Expanding Opportunities
Content Recorded and Published at WEFTEC in October 2024 In this episode of The Water Online Show: On Location, (now former) McCrometer President Pete Oveson dives into the company's story and recent developments shaping its future. He begins with an overview of...
Request More Information