Better Solutions for Reverse Osmosis Flow Measurement
The Importance of Measuring Reverse Osmosis Flow
Reverse osmosis (RO) is the process of running raw water through a system of membrane sheets that filter out suspended and dissolved particulates such as bacteria, salt, and other effluent materials, producing pure water as well as undesirable concentrate water. Reverse osmosis flow is often used in metals and mining, food and beverage, power generation, semiconductor electronics, pharmaceuticals, saltwater disposal wells for oil and gas, marine, hospitals, and drinking water treatment applications.
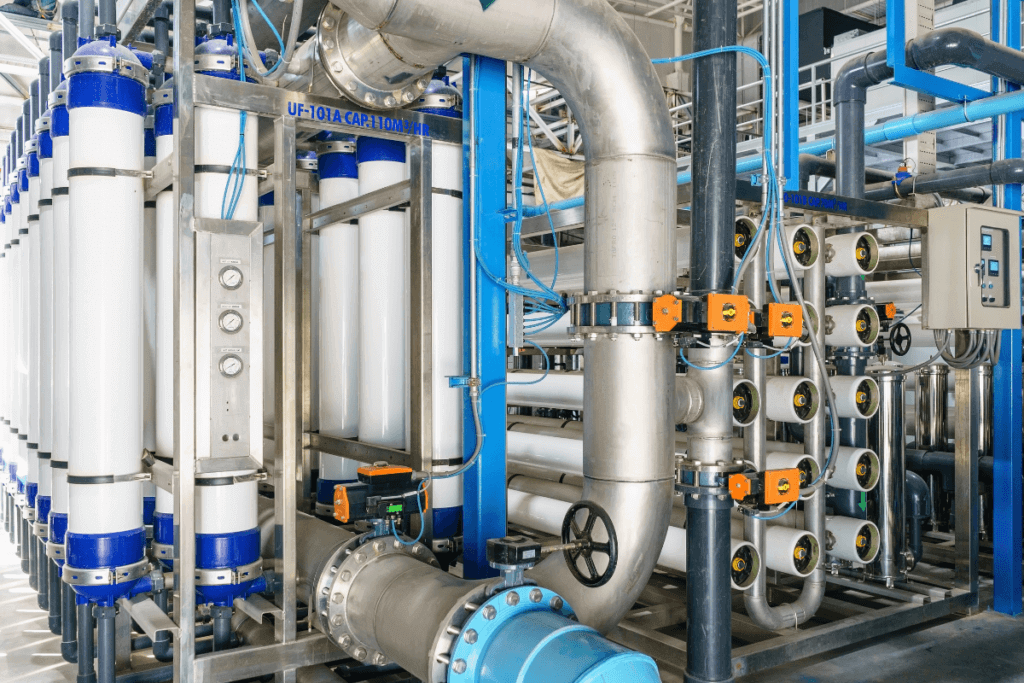
A water treatment facility’s reverse osmosis system.
Engineers and plant managers concerned with operational efficiency need to know quantities of raw water intake and pure water production from their reverse osmosis processes. It often requires a significant amount of power to run a reverse osmosis application so having consistent and reliable inlet and outlet flow data is imperative, especially when needing to report flow data to a regulatory body.
In geographic areas with high demand on the local water systems, reverse osmosis provides an efficient, sustainable method of water usage and recycling. It’s considered one of the “greenest” solutions for treating raw water for manufacturing processes, as well as for remedying industrial wastewater. Many industries measure initial raw water intake and pure water production as well as industrial effluent and recycled RO water that is returned to the manufacturing process. Measuring all points of the RO process provides data on operational efficiency and effectiveness as well as environmental accountability and regulatory compliance.
Raw Water and Effluent Flow Measurement Challenges
In many reverse osmosis applications, raw water is pumped from whatever body of water is available, which may be seawater, brackish water, sandy or silty water, or even a mixture of oil and water. When measuring at the inlet, often nearby a high-pressure pump, there’s the challenge of meter durability. Mechanical meters and turbines have moving parts that can corrode or require frequent maintenance to keep clean and free of debris. Effluent flow can contain harsh chemicals, mineral and metal particulates, and other hazardous components that can cause issues for less durable flow meters.
Sediment, particulates, or a dirtier flow can cause meters such as transit time ultrasonics to produce an inaccurate reading, whereas a dirty flow is well-suited to electromagnetic (mag) flow meters. McCrometer’s Ultra Mag® flow meter features a fusion-bonded epoxy coating rather than a traditional rubber or plastic liner, eliminating the possibility of tearing or delamination. Other mag meters on the market bearing traditional liners run the risk of it separating from the meter body and being sucked into the pump (and possibly damaging expensive equipment). The Ultra Mag has a lifetime guarantee against delamination, giving engineers and plant managers peace of mind as well as accurate, reliable flow measurement for the life of their RO process.
Pure Water Flow Measurement Challenges
Whereas the mag meter performs extremely well in harsh raw water applications, it simply cannot gain an accurate reading in pure water applications. The lack of impurities in the flow makes it impossible for the mag meter to receive adequate electromagnetic signals; this is consequently a limitation of the technology in this application.
A common metering choice for pure water is the ultrasonic meter, as both the transit time and Doppler clamp-on variations are amenable to the RO flow media. The ultrasonic provides accurate measurement, long lifespan, and is simple to install. However, the appeal of the convenient clamp-on ultrasonic poses potential problems for noisy applications with frequent foot traffic. Misalignment or irregular contact with the exterior of the pipe wall increases the possibility of sensor disruption and can cause a previously accurate meter to suddenly produce wildly inaccurate readings. In industries that are required to report flow data to regulatory bodies such as the Environmental Protection Agency (EPA), inaccurate and unreliable flow data is unacceptable. RO is an expensive process with a considerable amount of equipment nearby that can possibly cause vibrations and misalign the ultrasonic transducers, which require precisely spaced parallel placement to monitor the flow.
Alternately, the classic propeller meter, such as the Mc®Propeller flow meter, accurately measures pure water flow in RO applications. Ideal for placement at the transfer point of pure water, the McPropeller offers a ± 2% accuracy, long lifespan, and is an economical choice for customers concerned about budget.
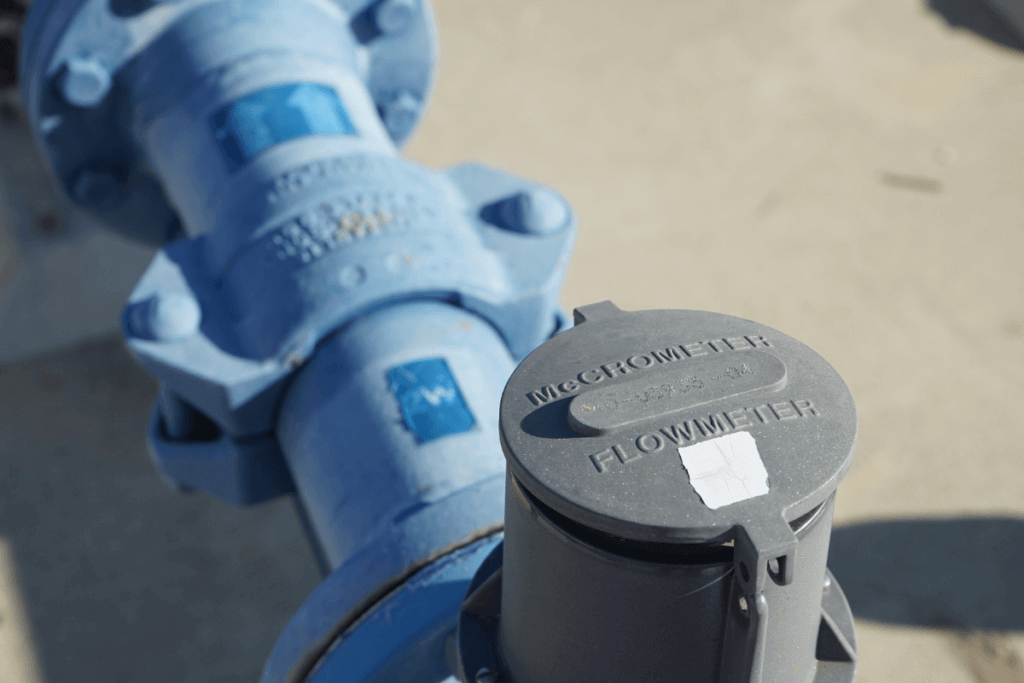
An McPropeller installed in a municipal water treatment application.
For engineers and users requiring higher accuracy, McCrometer’s Wafer-Cone® is a great off-the-shelf option offering ± 1% accuracy for line sizes 1” – 6” (25.4mm – 154.2mm). The Wafer-Cone also boasts a 25+ year lifespan and is a “set it and forget it” meter that provides accurate, reliable flow measurement for the lifetime of the RO operation.
Space and Weight Challenges
Many industries rely on RO as their chosen water treatment process for offshore operations, such as marine industrial applications, maritime transport, offshore oil drilling, and even the aerospace sector. Due to the nature of these applications, there are often space and weight restrictions that instill limitations when choosing a flow meter for these projects.
Ultrasonic flow meters require a fully developed laminar flow profile, meaning that most meters require at least 10 diameters upstream of meter placement and at least 5 pipe diameters downstream. Nearby noisy equipment or additional flow disturbers such as valves or elbows can add to that requirement. Required straight-run piping can add to the overall weight of a project as well as the required real estate; in retrofit applications, it can also require additional installation budget to reconfigure piping.
The Ultra Mag requires only 3D upstream and 1D downstream (wafer style 2”-3”) and 1D upstream and 0D downstream (flanged style 4”-48”) of most flow disturbers while still maintaining that ±0.5% accuracy for raw water inlet applications. For pure water applications, the Wafer-Cone requires only 1-3 diameters upstream and 1 downstream, depending upon nearby flow disturbers. The McPropeller normally requires 5 to 10 diameters upstream and 1 to 2 diameters downstream, but by installing a flow straightener or hex vanes upstream of the propeller to condition the flow, the requirements lessen to 1.5 straight pipe diameters upstream and 0-0.5 downstream. This makes the economical McPropeller a perfect choice for retrofit pure water applications with minimal existing straight-run pipe.
The Best Solutions for Reverse Osmosis Flow Measurement
When accuracy and reliability are critical, engineers and plant managers can’t be expected to compromise on durability and technical specifications. The best flow meter is the instrument that allows users to meet and exceed their project goals, sustainability objectives, and regulatory requirements. For additional information about the McPropeller, Wafer-Cone, or Ultra Mag, reach out to the McCrometer factory or contact your local authorized representative.
Related Posts
Featured Posts
Choosing the Right Non-Contact Flow Meters: A Quick Dive into Radar and Laser Technologies
When measuring open channel flow wastewater and stormwater, non-contact flow technology is the ideal method, able to provide an accurate velocity and flow rate. Especially in the wet weather season, non-contact flow technology greatly benefits open channel...
Meeting BABA Compliance And Expanding Opportunities
Content Recorded and Published at WEFTEC in October 2024 In this episode of The Water Online Show: On Location, (now former) McCrometer President Pete Oveson dives into the company's story and recent developments shaping its future. He begins with an overview of...
McCrometer, Inc. Announces Redesign of FlowComTM Digital Register
FOR IMMEDIATE RELEASE: September 3rd, 2024Contact: Aimee Davis, Vertical Marketing Manager, Agriculture McCrometer, Inc.AimeeD@mccrometer.com Hemet, Calif. – McCrometer, Inc., a globally recognized flow meter manufacturer, today announced the launch of their...
Request More Information