Thermal Steam Injection in Enhanced Oil Recovery: A V-Cone Oil and Gas Application
Thermal steam injection in enhanced oil recovery (EOR) is a popular method for third stage oil production, especially for highly viscous oil. Tough environments like shale oil reservoirs that require thermal methods for oil recovery require durable flow meters that tolerate high-pressure flow conditions. The V-Cone®, ideal for many oil and gas applications, is regularly selected for steam measurement in thermal EOR due to its 25+ year lifespan, accuracy, and sheer rugged design.
So, where does the V-Cone perform best in a thermal steam injection application? We spoke to our Canadian channel partner in Alberta, Tundra Process Solutions, LTD., to get their insight on V-Cone for EOR.
A Tough Application
While there are a variety of EOR methods employed in oil and gas production, such as gas lift, chemical injection, and water injection, steam is often used for heavier crude in order to heat the oil, decreasing its viscosity, and enabling it to flow to the surface. Steam injected into the reservoir isn’t necessarily high-quality steam. It may be poorer quality and unsaturated, at 70-80% before a steam separator. The potential for entrained steam condensate (liquid) requires a flow meter that can measure dual-phase media. Additionally, entrained steam condensate may damage other meter types, necessitating meter replacement.
The V-Cone is known for accurately measuring wet gas, or in this case, steam for injection. Designed with no moving parts, the V-Cone can also be constructed from a range of standard and exotic materials that are corrosion-resistant and NACE MR0175 compliant. This customization is what makes the V-Cone a smart choice for metering projects measuring steam and other fluids where chlorides and hydrogen sulfide (H2S) may be present, also known as sour service, a flow media that can cause stress-induced cracking in certain metals.
The V-Cone vs. Other Metering Technologies
Steam injection is an application known for running flow media upwards of 550°F and high PSI, requiring a meter with flanges of a significant weight, such as 1500lb RTJ flanges. Other meters accommodating these flow conditions can become heavy and expensive and require long manufacturing lead times. Especially in offshore or subsea steam injection applications, the V-Cone’s minimal-to-no straight-run requirements save on space and weight.
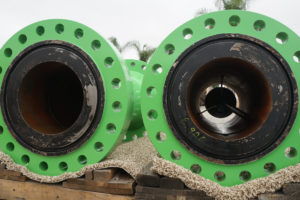
A V-Cone with RTJ flanges.
Other metering technologies can be used in steam injection applications, but often struggle with unsaturated steam. Poor-quality steam can cause havoc with ultrasonic meters, as liquid entrained in steam can interrupt the path of a sound signal, cause erroneous readings, and produce inaccurate and noisy measurement.
Orifice plates are a common option for metering in EOR, but liquids can dam up with this type of meter, and at high temperatures and pressures, dull the sharp edges of the orifice plate rendering measurement inaccurate. Additionally, high permanent pressure losses, straight-run requirements, entrained liquids, and short expected lifespan are additional challenges with these meters in this application.
The vortex flow meter is often a contender for EOR measurement, but operators may encounter problems with blocked vortex-sensing ports; if the sensing ports of the vortex meter become blocked, the entire process will need to be shut down for meter maintenance. In a cyclical steam injection process, where steam injection can sometimes last 2-3 months, unexpected downtime drives revenue losses and meter maintenance losses, among other inconveniences. Additionally, many vortex meters are limited to 1500lb pressure lines, which may not fit specifications for some steam injection applications.
Where the V-Cone Wins
Due to the highly viscous oil that thermal steam injection is stimulating, the V-Cone is typically utilized for measurement on the injection side of the project. On the production side, the fluid is an emulsion mix of oil and water, often not measured until separated.
One of Tundra Process Solutions’ customers installed 50+ Wafer-Cone® flow meters in an EOR project to accommodate the declining production rate over time on their wells. By keeping their wells on a minimal decline curve, the customer was able to increase the injection flow rate by defined controlled increments in order to maintain oil recovery; furthermore, by the possibility given by the interchangeable cone in their Wafer-Cones, they could accommodate the changing flow conditions. Each replacement cone was calibrated with a different beta ratio, allowing the customer to accurately measure the wide range of flow without purchasing new meters. The V-Cone can accurately measure the flow from the day EOR operations begin, until the day the well dries up, with maximum efficiency.
The unprecedented accuracy of the V-Cone and Wafer-Cone allowed the customer to monitor their injection rates and make informed decisions during daily operations; depending upon well production rate and composition, the need for steam injection changed.
The Team Behind the V-Cone
Tough flow projects require unique solutions, but they also require effective communication and expertise from the flow meter manufacturer to understand the application, the customer’s project goals, and how best to provide a lasting and beneficial metering solution. McCrometer strives to be more than simply a meter supplier. Our goal is to be our customers’ advisor and partner from project inception to ongoing metering champion.
To start your conversation with our flow meter experts, and to share your metering project with our team, visit www.mccrometer.com/oil to learn more.
Related Posts
Featured Posts
3 Reasons Why Budget-Focused Farmers Invest in Integrated Telemetry
Allocating budget to flow technology may seem unjustifiable when funds are tight; flow meters and their electronics may already be installed, giving no reason to replace or add additional units when the current solution is in fine working condition. However, flow...
Small Package, Big Impact: The Importance of Desiccant Cartridge Maintenance
You’ve likely seen a desiccant cartridge, in the form of the small silica gel packet accompanying food products, or the activated carbon packet at the top of pharmaceutical bottles. It’s also commonly used in electronics and near sensors, especially for...
Meeting BABA Compliance and Expanding Opportunities
Content Recorded and Published at WEFTEC in October 2024 In this episode of The Water Online Show: On Location, (now former) McCrometer President Pete Oveson dives into the company's story and recent developments shaping its future. He begins with an overview of...
Request More Information