The V-Cone and External Vibrations
Contrary to the popular Beach Boys song, vibrations aren’t always good – especially when they interfere with the functionality of your flow meter. In busy spaces where neighboring equipment gives off varying frequencies, having a flow meter that can mitigate surrounding noise and provide accurate, reliable flow readings are critical to achieving operational efficiencies.
The V-Cone® does just that – despite the complexities of many flow applications, the V-Cone stands up to vibrational resonance.
Here’s the basic overview.
What Causes Vibrational Resonance?
Typically, in many oil and gas and industrial applications, the meter is close in proximity to equipment like pumps, dynamic control valves and other mechanical hardware emitting cyclic noise or significant vibrational resonance.
This tends to occur more in certain applications experiencing a high pressure, high-velocity flow such as a compressor discharge, or in high-pressure gas lines.
Vortex shedding frequencies occur when flow passes over an obstruction such as a butterfly valve. This can cause vibrational resonance, especially if the obstruction isn’t mounted rigidly.
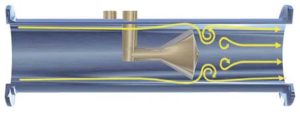
The centrally-located cone directs flow to the outside wall, effectively conditioning disrupted flows.
Planning for Vibrational Resonance in Your Flow Project
Often, the engineers and operations professionals managing a flow measurement project cannot perfectly predict what acoustics and frequencies will be present near their installation site – and we get it! Vibrational resonance is a very complex subject, and large flow projects rarely have one person managing every aspect of the project design. Many professionals with niche expertise come together to provide their recommendations for the pump, the securing and dampening of the pipes, the meter, and more – and the complexity of planning can obscure the big picture of how the surrounding environment will affect the meter.
Knowing what vibrations exist and what equipment is articulating at certain frequencies and amplitudes prior to implementing a meter is often extremely difficult. It’s often discovered post-mortem once a part rattles loose in the equipment, causing the need for shutdown and repair.
Implementing a meter that withstands whatever vibrational resonance is nearby is a must to keep your pipeline operating.
How the V-Cone Accounts for Vibrational Resonance
The structure of the V-Cone, including the vertical and horizontal supports, is built to withstand external vibration. The V-Cone’s customizable nature allows it to meet demanding application requirements. In addition to a wide variety of exotic materials available for manufacturing, the V-Cone can also be modified in design, such as a reduction of the mass of the cone, to keep the meter as light and rigid as possible. Depending upon the demands of the application, a variety of gussets are included to support the cone and provide durability, including pin gussets on small line size meters, and pipe gussets on larger line sizes. The gussets support the cone in any condition; the end goal is always the same, but the method in which the McCrometer engineering team achieves that goal varies based on the customer’s flow conditions, line size, application, and more.
Not all applications are the same, and the V-Cone is not an “off the shelf” product. The flexibility of the V-Cone allows it to maintain its durability and 25+ year lifespan in the toughest and most challenging environments, including those with external vibrations.
The Challenge of Vibrational Resonance
McCrometer engineered a custom V-Cone design for a project in 2018, when a customer had purchased a competitor’s cone-style meters for a natural gas application and due to the high-pressure, high-velocity flow properties, two of those cone meters failed.
This gave McCrometer an opportunity to work with the midstream gas customer on a solution for their 16” diameter line size, resulting in the engineering, development, and testing of various gusset designs and parameters in which they’re to be used. In order to maintain the rigidity of the cone and withstand the surrounding external vibrations (exacerbated by the high pressure, high velocity of the natural gas flow), McCrometer installed three V-Cones using our patented design incorporating pipe gusset supports both upstream and downstream of the cone. This design had not yet been implemented in V-Cones of that pipe diameter until this project.
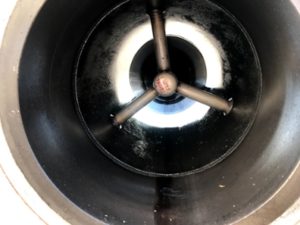
A close-up of the three pipe gussets on one of the 16” diameter V-Cones.
A year after the meters were installed, the oil and gas customer reported the custom V-Cones operating as intended, reading accurately and withstanding surrounding vibrational resonance.
Getting Your Challenging Flow Project Started
The McCrometer engineering team likes a challenge and enjoys collaborating with customers to provide unique and custom flow measurement solutions. Our goal is to help you meet project goals and get you the flow data you need to make informed decisions about daily operations.
To get started on a V-Cone quote or to learn more about our metering solutions, check out the V-Cone product page.
Related Posts
Featured Posts
Small Package, Big Impact: The Importance of Desiccant Cartridge Maintenance
You’ve likely seen a desiccant cartridge, in the form of the small silica gel packet accompanying food products, or the activated carbon packet at the top of pharmaceutical bottles. It’s also commonly used in electronics and near sensors, especially for...
Choosing the Right Non-Contact Flow Meters: A Quick Dive into Radar and Laser Technologies
When measuring open channel flow wastewater and stormwater, non-contact flow technology is the ideal method, able to provide an accurate velocity and flow rate. Especially in the wet weather season, non-contact flow technology greatly benefits open channel...
Meeting BABA Compliance and Expanding Opportunities
Content Recorded and Published at WEFTEC in October 2024 In this episode of The Water Online Show: On Location, (now former) McCrometer President Pete Oveson dives into the company's story and recent developments shaping its future. He begins with an overview of...
Request More Information