Stay Grounded: Avoiding Mag Meter Mishaps
Electromagnetic (mag) meters are a desirable metering choice for their incredible accuracy and low to no maintenance required over its lifespan. Operating with no moving parts, the appeal is high – however, the ability to troubleshoot in-field is challenging and time-consuming. Luckily, there’s a major contributing factor in installing an effective mag meter that can set you (and your operations) up for success: grounding.
Mag Meter Grounding in a Nutshell
Mag meters operate based on Faraday’s Law of Electromagnetic Induction, which says that a conductive media moving through a magnetic field will produce a voltage proportional to the velocity of that conductor.
The conductive media is water, and as it flows through a McCrometer mag meter it can effectively and accurately be measured. Frequently, however, there are environmental or electrical elements near the meter that may interfere with its ability to communicate with the coils and electrodes inside the body of the mag.
Grounding is then necessary to stabilize the meter and lessen the surrounding electrical “noise” interference and connect the meter to a stable connection (not necessarily the earthy ground).
Is Grounding Always Needed?
McCrometer provides grounding rings with most mag meters offered and recommends them as a “best practices” step during installation. Grounding rings can often be neglected, or installed incorrectly, or there are issues that arise during the installation process.
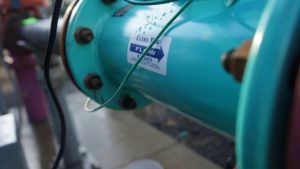
A McCrometer Ultra Mag with grounding rings.
However, when installed correctly, grounding rings ensure that your mag meter is operating as it should, unaffected by surrounding electrical noise. Think of grounding rings as a cheap form of insurance – you’d rather ground your mag meter during install than realize you need to ground your meter after it has been buried, or the vault has been closed. Installing grounding rings after the fact can cause delays in operations, costly (and unnecessary) construction, and make you question the integrity of the flow data you collected. Grounding your meter during install allows you to measure with confidence knowing that your flow data is accurate.
Do Your Homework
Prior to installing your mag meter, do some additional scouting of the installation site. Is the environment new construction or an older location for retrofit? Conduct an electrical survey to ensure everything is up to code. This can save a lot of work down the road and possibly help you avoid future issues with the meter’s electronics. If the site location is in an electrically dense environment, you may have issues running longer mag meter cable runs to a control center.
When you have your meter on site and are ready to install, some extra due diligence can work in your favor. If you’re installing an insertion mag meter, you can actually test its functionality prior to hot-tapping it into your pipeline. Conduct the bucket test by submerging the insertion meter in a bucket of water and plugging it in. You’re then able to test the electrodes, the empty pipe sensor, and get a baseline for the meter’s performance in an isolated environment versus a pipeline with electrical noise. This pre-installation functionality testing is a way to diagnose any issues prior to the effort of installing the meter in your pipeline. For full-bore mag meters, power up the converter prior to install and configure the settings to meet your needs prior to install.
Some Additional Mag Meter Pro Tips
Tip #1: If you’re installing a mag meter into a potable water system, don’t forget to disinfect the product and sterilize the sensors prior to install. This ensures that any dust or grime from the packaging and install site don’t make it into your pipeline along with the meter.
Tip #2: More often than not, there’s an entire team of professionals handling a metering project, like the engineers who selected the meter, the purchasing department who placed the order, the crew who handles the pipe installation, and the operator who interacts with the meter and data on a day-to-day basis. Don’t hesitate to inform your team that the experts at the factory are available to assist with questions throughout the entire process.
Tip #3: Your mag meter converter comes pre-configured, so if you plan to connect your mag to your existing SCADA system, you’ll first need to match up the scaling. Your data management system will need to know the full-scale value of your mag meter in order to receive the flow data.
For more information on grounding, please refer to the IOM associated with your mag meter or contact the factory.
Related Posts
Featured Posts
3 Reasons Why Budget-Focused Farmers Invest in Integrated Telemetry
Allocating budget to flow technology may seem unjustifiable when funds are tight; flow meters and their electronics may already be installed, giving no reason to replace or add additional units when the current solution is in fine working condition. However, flow...
Small Package, Big Impact: The Importance of Desiccant Cartridge Maintenance
You’ve likely seen a desiccant cartridge, in the form of the small silica gel packet accompanying food products, or the activated carbon packet at the top of pharmaceutical bottles. It’s also commonly used in electronics and near sensors, especially for...
Meeting BABA Compliance and Expanding Opportunities
Content Recorded and Published at WEFTEC in October 2024 In this episode of The Water Online Show: On Location, (now former) McCrometer President Pete Oveson dives into the company's story and recent developments shaping its future. He begins with an overview of...
Request More Information