Calibrating Gas Meters in Water
McCrometer’s V-Cone® flow meter, patented in 1985 and popular for industries such as oil and gas, offers the benefit of a calibration from the factory prior to shipping to the installation site. This calibration, testing the meter against the entire Reynolds range, is a quality assurance completed at one of McCrometer’s NIST-traceable flow labs – and is indeed completed using water as the flow media.
Many of McCrometer’s customers have inquired about the water calibrations, especially for meters that will ultimately be used for gas applications.
So – if your meter is used for gas, why do we calibrate in water?
Let’s review.
Meter Calibration: An Overview
Calibration is the process of checking, by comparison with a standard, the accuracy of a measuring instrument. In plain terms, it’s the configuration of a V-Cone to produce a result for a sample within a desired flow range.
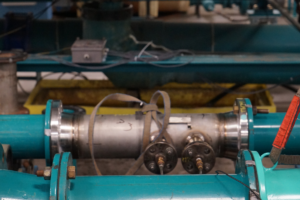
A V-Cone during the calibration process at McCrometer’s NIST-traceable flow lab in Hemet, CA.
The overall goal is to determine the discharge coefficient (Cd) of the meter. The Cd is a number used to characterize the flow and pressure loss (head loss) behavior of equipment in a fluid system. The Cd is dependent on the Reynolds number (Re), not just density or viscosity. Density and viscosity are considered with the Reynolds number.
McCrometer aims to calibrate over the complete range of the customer’s application, and if not able to cover the complete range, there may be a reduction in accuracy.
The equation for the Reynolds number is:
In many cases the differential pressure (DP) and the flow rate generated during calibration will not match that of the application. McCrometer attempts to match only the Reynolds number, not the DP and flow rate. The practice of matching the viscosity, or fluid density, of an application can add significant costs for a marginal improvement in accuracy.
Water as the Calibration Media
Flow meter calibration means that you receive a flow meter that meets McCrometer’s published product specifications, including up to ± 0.5% accuracy and ± 0.1% repeatability. Certain fluids and Reynolds numbers may require specific calibrations to achieve this accuracy.
If there is a gas application and it has an exceptionally high Reynolds number, such as natural gas applications, McCrometer will not calibrate in water and will send the meter to a 3rd party calibration lab for gas calibration. However, the majority of standard-sized V-Cones are calibrated in one of our on-site flow labs.
Initial Calibration
McCrometer’s calibration is performed using standards traceable to the National Institute of Standards and Technology (NIST). McCrometer maintains a Certificate of Accreditation to ISO/IEC 17025.
McCrometer primarily utilizes gravimetric and dynamic head calibration in our flow labs. The McCrometer gravimetric test method is based on ASME MFC-9M-1988: Measurement of Liquid Flow in Closed Conduits by Weighing Method. Following this methodology, a mass of water flowing through the test meter is collected and measured over a measured time interval.
The McCrometer dynamic head calibration method whereby incremental changes of volume in a supply tank are correlated to instantaneous rates of flow at the meter, though proprietary, is based on well-established physical principles and relationships. The method is further supported by a complete and detailed uncertainty analysis as well as traceability to NIST pressure, mass, time, and temperature standards.
Recalibrating Gas V-Cones
Certain regulatory agencies may require recalibration or validation of the V-Cone. A recalibration cannot be done in field; since recalibration is the repetition of the original calibration, that process must be completed in one of McCrometer’s NIST-traceable flow labs. Recalibration requires the customer to remove the flow meter from the line and ship it back to McCrometer. McCrometer will then clean the flow meter, follow all regulatory requirements, accommodate any changes to the customer’s process conditions, recalibrate, and return it to the customer.
EPA 40 CFR 75 App D requires flow meters to be calibrated over the complete flow range, with a minimum of three data points at the maximum, minimum, and mid-flow rates. The accuracy requirement is 2% of full-scale flow, and recalibration periods range from annual recalibration to once every five years, depending upon the situation.
Whereas recalibration cannot be completed in-field, validation can. Recalibration ensures accuracy, whereas validation confirms if the output is consistent and that the V-Cone doesn’t have excessive erosion. A field validation of the V-Cone transmitters is also available, to ensure optimal operating conditions.
Calibration (and Recalibration) Performed by the Professionals
The V-Cone is a durable, wear-resistant flow meter, and many customers don’t opt for recalibration or validation. We recommend that those customers wanting recalibration or validation consult McCrometer to discuss options, as the V-Cone engineers and technical support professionals are highly trained in inspection and measurement to provide calibration and recalibration services.
Our engineers hold specialized knowledge and experience about V-Cones for gas measurement, and specifically achieving the precision accuracy required for the application.
For more questions about calibrating gas meters in water, reach out to the McCrometer professionals at vconesupport@mccrometer.com
Related Posts
Featured Posts
Small Package, Big Impact: The Importance of Desiccant Cartridge Maintenance
You’ve likely seen a desiccant cartridge, in the form of the small silica gel packet accompanying food products, or the activated carbon packet at the top of pharmaceutical bottles. It’s also commonly used in electronics and near sensors, especially for...
Choosing the Right Non-Contact Flow Meters: A Quick Dive into Radar and Laser Technologies
When measuring open channel flow wastewater and stormwater, non-contact flow technology is the ideal method, able to provide an accurate velocity and flow rate. Especially in the wet weather season, non-contact flow technology greatly benefits open channel...
Meeting BABA Compliance and Expanding Opportunities
Content Recorded and Published at WEFTEC in October 2024 In this episode of The Water Online Show: On Location, (now former) McCrometer President Pete Oveson dives into the company's story and recent developments shaping its future. He begins with an overview of...
Request More Information