5 Flow Applications for Power Generation Plants: Gaining Efficiency through Water Measurement
1. Raw Water Supply
What It Is
Raw water supply must undergo treatment before being turned into steam for turbines at a power plant. Phase changes can cause buildup in piping systems if raw water isn’t treated; in addition to groundwater or surface water sources such as lakes and rivers, seawater is also a popular raw water supply. Seawater will need to undergo a desalination process in addition to treatment before becoming feed water for the turbines.
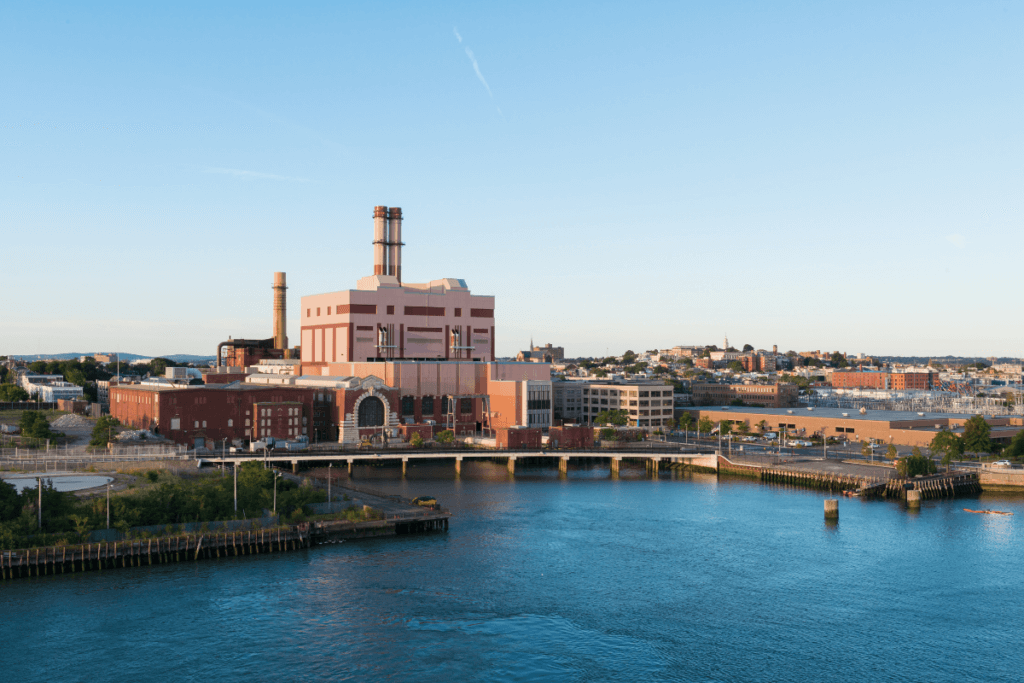
A power plant near a raw water source.
Challenges of Measuring Raw Water Supply
Sediment, such as sand or silt, can cause corrosion in the line and affect a mechanical meter’s accuracy and lifespan. You never quite know what you’re getting with raw water, and particulates as well as possible air bubbles in the line can make measuring with a meter like an ultrasonic problematic, as ultrasonic energy cannot pass with heavily contaminated flow media. Seawater can cause corrosion for many meters, causing buildup or corrosion, affecting meter accuracy and reliability. Raw water supplies are sometimes located some distance from the power plant, and without a guaranteed power source, so a meter offering battery-power and automated data collection is needed as well.
The Ideal Meter
For raw water supply that contains little to no debris in the flow, a propeller meter such as the Mc®Propeller can get the job done. However, for seawater, it’s recommended that a flow meter such as the Dura Mag™ or Ultra Mag® electromagnetic (mag) flow meters be installed. Both of these full-bore mag meters have the UltraLiner™, McCrometer’s proprietary fusion-bonded epoxy that performs well measuring caustic flows and resists corrosion. Unlike traditional mag meter liners, there is no risk of delamination or tearing which might clog the line or pump, necessitating expensive repairs. Additionally, the Dura Mag and Ultra Mag offer Hastelloy electrodes, preventing any buildup or corrosion and ensuring accurate, repeatable measurement.
For remote raw water applications, the ProComm GO™ converter offers battery power as well as AC and DC power and is AMI/AMR compatible. Telemetry solutions are also available, as it 4-20mA pulse output and other communication protocol.
2. Feed Water Supply
What It Is
Feedwater is the product of the raw water that’s been treated to remove impurities and prevent buildup. It is turned into steam in the boiler and is used to power the steam turbine, creating electricity.
Challenges of Measuring Feed Water Supply
Feedwater flow meters are often installed near a pump, so meters with a liner may delaminate or tear and clog the line and damage expensive pipeline equipment. The flow media itself is pure water, which offers no conductivity for measurement devices such as electromagnetic flow meters to produce readings. Often in feed water applications, there is little straight-run pipe available, due to centralized location between the raw water treatment facilities and the boiler. Frequently, feed water flows through smaller pipelines and has low flow rates.
The Ideal Meter
Due to the purity of the flow, mag meters, and doppler ultrasonics won’t fit this application. Ultrasonic transit-time meters, vortex, or a differential pressure meter such as the V-Cone® or Wafer-Cone® are better solutions. For lower velocity or changing flow conditions, the V-Cone is a great solution due to its 10:1 turndown (20:1 with stacked transmitters). A propeller meter, like the McPropeller, is a low-cost, reliable option for flow projects running feed water at a low enough temperature; the McPropeller tolerates a temperature up to 160° F (71° C).
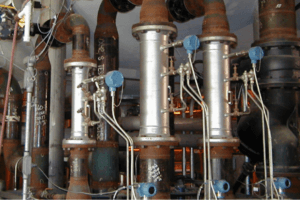
Multiple vertically-installed V-Cones.
3. Condenser Water
What It Is
Steam leaving the turbine enters a condenser in order to phase change and be recycled. This is done by way of cooling water flowing through condenser tubes to cool the steam and produce condenser water. The water is then sent back to the boiler to become steam again and fuel the steam turbine to create electricity.
Challenges of Measuring Condenser Water
In any steam-generated power plant, efficiency and accurate flow measurement is the main goal. Combined-cycle power plants are more efficient than coal-fired and natural gas plants, so quantifying efficiency and maintaining a small carbon footprint is the goal for plant managers and instrumentation engineers. Condenser water may also be treated to prevent buildup of microbiological growth to decrease the frequency of routine tube and meter cleaning.
The Ideal Meter
The Ultra Mag’s custom lay lengths make the meter retrofit-friendly and allow it to contribute to a small pipeline with its small physical footprint. Requiring only 1 pipeline diameter upstream of most flow disturbers, and resistant to corrosion and buildup, the Ultra Mag provides worry-free, accurate measurement.
4. Cooling Tower Water
What It Is
Once the condenser water has cooled the steam, it flows back into a cooling tower to remove the heat before entering the condenser tubes again, in a process referred to as a recirculating cooling system. In the cooling tower, the heated water enters the tower at the top and moves its way downward while air blows upward. Temperature transference occurs, with the water cooling down and the air becoming warmer. The now-cooled water then flows back into the condenser to cool more steam flowing out of the turbine.
Challenges of Measuring Cooling Tower Water
Compared to HVAC cooling towers, the volume of cooling tower water in this application is greater, and measurement is more critical. The chemistry of cooling water has the potential to change, causing scaling and functional problems for mechanical meters. Additionally, biofouling can spur the need for chemical injection to manage microbiological growth, which may cause deterioration of certain measurement devices.
The Ideal Meter
The Ultra Mag and FPI Mag meters work well in cooling tower water applications, as they’re unaffected by caustic flow media. Maintaining accuracy up to ±0.5%, these mag meters provide flow measurement for the life of the facility, despite changing water chemistry. For shutdown turnaround management professionals, the FPI Mag’s hot-tappable installation comes in handy, as there’s no need to shut down the cooling tower to initially install the meter or remove the meter for maintenance. Additionally, McCrometer’s low lead times and USA-based manufacturing ensure that when a power plant needs a flow meter, they can obtain one without supply-chain delays.
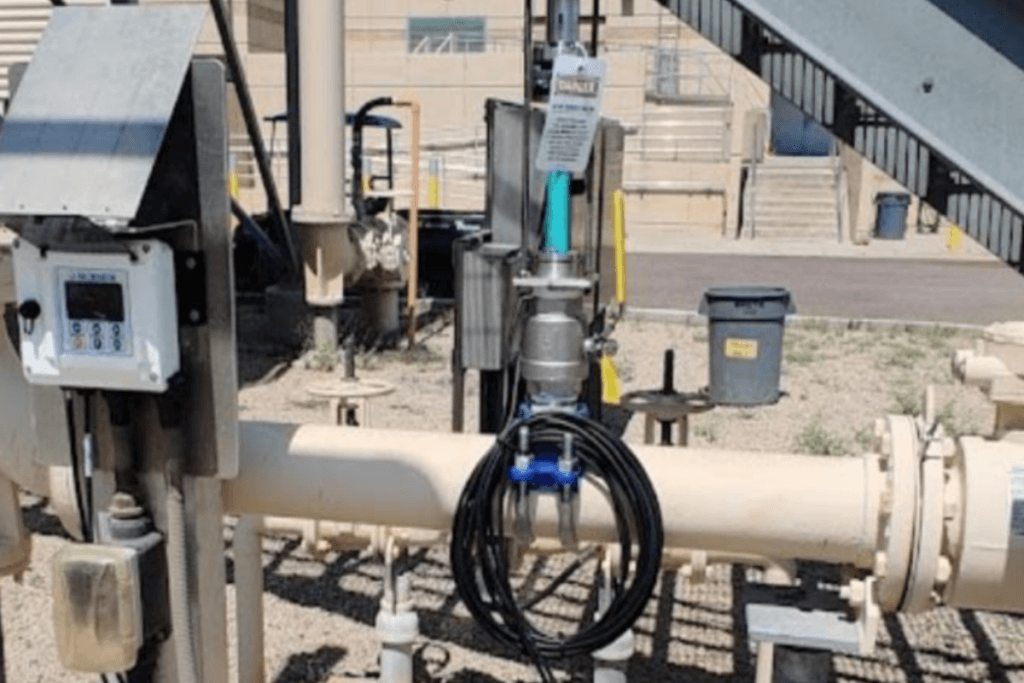
An FPI Mag and ProComm™ converter installed, measuring water.
5. Effluent Water
What It Is
Wastewater discharge from a power plant is generated from chemical pollutants treating raw water sources, air pollution controls, and more. Depending upon the type of power plant, effluent amounts may vary. Effluent water can contain nickel, bromide, selenium, and various other chemicals and dissolved metals that have serious side effects on the health and safety of nearby communities and have ecological impacts. For these reasons, effluent is highly regulated by the state as well as the EPA. Flow measurement points can include leachate and effluent ponds, cooling water effluent, and more.
Challenges of Measuring Effluent Water
Since wastewater discharge is a heavily regulated flow media, ensuring accurate, repeatable measurements is critical. Additionally, a flow meter that can withstand the variety of corrosive, caustic chemicals and particulates is necessary, as effluent can range from seawater to coal pile runoff.
The Ideal Meter
Mag meters shine in this application – the Ultra Mag’s fusion-bonded epoxy and stainless-steel electrodes resist corrosion and withstand harsh effluent flows. Additionally, the battery-powered electronics, the ProComm GO, allow the full-bore meter to be installed further away from a reliable power sources. For retrofits wanting to avoid shutting down the pipeline, cutting and welding flanges, and overall system downtime, the FPI Mag’s hot-tappable installation makes installation easy and reduces overall costs by up to 45%. Whereas the Ultra Mag offers sizes up to 48” (1219mm), the FPI Mag can be manufacture up to 120” (3048mm), an economical choice for considerable large nominal pipe size flow projects.
Related Posts
Featured Posts
3 Reasons Why Budget-Focused Farmers Invest in Integrated Telemetry
Allocating budget to flow technology may seem unjustifiable when funds are tight; flow meters and their electronics may already be installed, giving no reason to replace or add additional units when the current solution is in fine working condition. However, flow...
Small Package, Big Impact: The Importance of Desiccant Cartridge Maintenance
You’ve likely seen a desiccant cartridge, in the form of the small silica gel packet accompanying food products, or the activated carbon packet at the top of pharmaceutical bottles. It’s also commonly used in electronics and near sensors, especially for...
Choosing the Right Non-Contact Flow Meters: A Quick Dive into Radar and Laser Technologies
When measuring open channel flow wastewater and stormwater, non-contact flow technology is the ideal method, able to provide an accurate velocity and flow rate. Especially in the wet weather season, non-contact flow technology greatly benefits open channel...
Request More Information