3 Things You Didn’t Know about the V-Cone
You’ve seen our spec sheets. You’re familiar with our website. But how many fascinating stories of V-Cone® applications have you heard? We’re here to share 3 little known facts about the V-Cone, from our V-Cone Applications Engineering Manager.
A Strong Solution
One of the most customizable components of the V-Cone is the material construction; most V-Cones are manufactured from popular metals or more exotic metals, but one little-known fact is that we can manufacture V-Cones out of titanium.
The McCrometer engineers have worked on a handful of titanium V-Cone projects and although the manufacturing is more complicated than other material manufacturing, it’s beneficial to our customers. Machining titanium can produce shavings that ignite, so extra precaution needs to be taken during machining, including the use of high-pressure coolant and specially coated tools to protect the material. Additionally, welding needs to take place in a neutralized environment, such as an argon bubble or other shield gas, as titanium is a reactive metal sensitive to oxygen.
Titanium is beneficial for applications with a highly corrosive fluid or surrounding environment, especially if that application has space and weight concerns. For instance, desalinization or seawater piping systems on floating platforms or ships would require the low-density metal for V-Cone material construction. Titanium is lighter than steel, corrosion-resistant, and long-lasting, a perfect choice for a V-Cone which on average has a lifetime of 25+ years.
Large V-Cones
Our customers are familiar with our large line size V-Cones (just follow our social media accounts for regular updates!) but not many are aware of our V-Cones of titanic proportion. Manufactured in 2014, our largest spool-piece V-Cone was an epic 78” meter composed of carbon steel and stainless-steel cone measuring propylene gas. Due to its large manufactured size, the meter underwent three non-destructive tests: radiographic testing, physical testing, and hydrostatic testing.
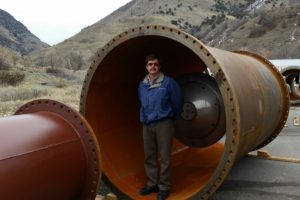
One of McCrometer’s Applications Engineers standing in the 78” V-Cone.
Unique V-Cone Customer Application
V-Cones are popular in a handful of oil and gas applications such as gas lifts, booster stations, enhanced oil recovery, and more – but often we don’t cover the more esoteric applications where the V-Cone can really provide measurement benefits. In an experimental project, a 1” V-Cone was manufactured for installation inside a nuclear reactor adjacent to a fuel source. This stainless-steel meter was a custom length and had multiple custom pressure taps measuring cooling water in a counter-flow heat exchanger.
Part of what makes the V-Cone an ideal meter for cutting-edge projects is the level of customization available; meeting project specs and offering unprecedented durability and accuracy makes the V-Cone an ideal choice for any challenging application.
…And More!
We limited ourselves to 3 unique facts about the V-Cone that illuminate some exceptional customer success stories, but there are most certainly more. Each engineering professional on the McCrometer team has worked closely with various customer projects, and has their favorite stories of unique meters, challenging projects, and shock-and-awe moments.
If you’re interested in sharing your favorite V-Cone success story, email our team at marketing@mccrometer.com!
If you’re interested in becoming our next favorite V-Cone success story, request a quote or email our V-Cone Applications Engineering team at vconerfq@mccrometer.com
Related Posts
Featured Posts
Choosing the Right Non-Contact Flow Meters: A Quick Dive into Radar and Laser Technologies
When measuring open channel flow wastewater and stormwater, non-contact flow technology is the ideal method, able to provide an accurate velocity and flow rate. Especially in the wet weather season, non-contact flow technology greatly benefits open channel...
Meeting BABA Compliance And Expanding Opportunities
Content Recorded and Published at WEFTEC in October 2024 In this episode of The Water Online Show: On Location, (now former) McCrometer President Pete Oveson dives into the company's story and recent developments shaping its future. He begins with an overview of...
McCrometer, Inc. Announces Redesign of FlowComTM Digital Register
FOR IMMEDIATE RELEASE: September 3rd, 2024Contact: Aimee Davis, Vertical Marketing Manager, Agriculture McCrometer, Inc.AimeeD@mccrometer.com Hemet, Calif. – McCrometer, Inc., a globally recognized flow meter manufacturer, today announced the launch of their...
Request More Information