3 Challenges of Ballast Water Flow Measurement
What is Ballast Water?
In the marine industry, ballast water is intake water on board a ship to maintain its stability and balance during voyages. Seawater is pumped into ballast tanks when the ship is not carrying a full cargo or needs to adjust its weight distribution, and then discharged at the destination or at another port when cargo is loaded.
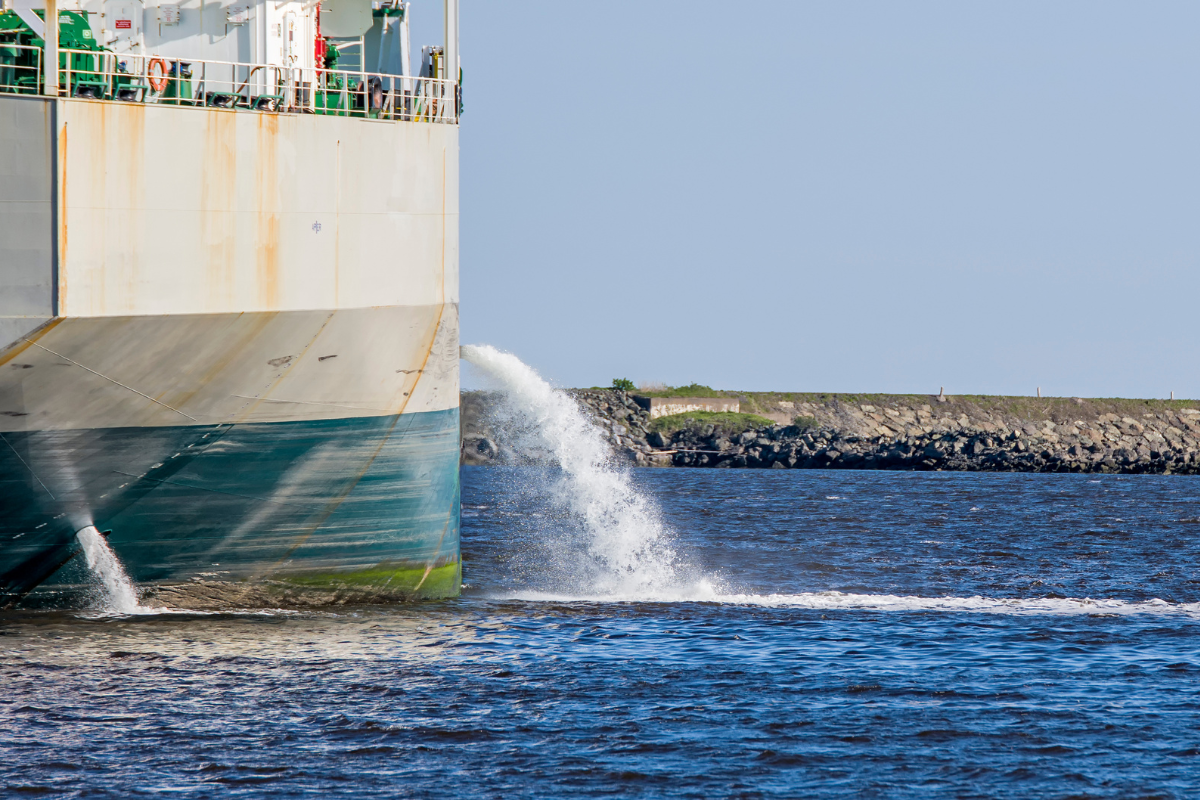
A ship emptying ballast water.
Ballast water is a potential carrier of aquatic organisms, such as bacteria, viruses, algae, and small animals, which can be harmful to the environment and to human health. When discharged into new environments, ballast water can introduce invasive species that disrupt local ecosystems, leading to significant economic and ecological damage.
Challenge #1: Ballast Water Regulations
Due to the potential economic and ecological damage that ballast water discharge can inflict, the International Maritime Organization (IMO) has developed regulations to control the discharge of ballast water and minimize these risks. These regulations require ships to install treatment systems to remove or neutralize harmful organisms before discharge and follow specific procedures for ballast water management.
All ships must implement a ballast water management plan, which includes keeping record books and strict procedures and standards to meet the stringent IMO regulations. Ships are required to implement accurate and reliable equipment for measuring the ballast water update and discharge flow rate. IMO guidelines also specify that flow meters used should be calibrated and maintained regularly to ensure their accuracy and reliability. Additionally, the guidelines also recommend that the flow meters connect to the ship’s monitoring and control systems to facilitate data recording and analysis.
Overall, the use of flow meters is an integral part of proper ballast water management, as they ensure compliance with international regulations and minimize the risk of introducing invasive species.
To meet these stringent regulations, operators and technicians aboard a ship often face the challenge of securing and maintaining a flow meter that is dependable, accurate, and can provide them with the data they need to inform daily decisions about ballast water intake, movement, and discharge.
Challenge #2: Weight, Space, and Accuracy Concerns
New designs and projects are often easier, but for retrofit projects, specifying a flow meter that meets regulatory requirements and doesn’t require a complete rebuild of a ballast water system can be tricky. Often, flow meters with significant straight-run requirements, such as orifice plates, ultrasonics, or vortex meters, can burden an already tight space and cost both time and money to accommodate. Not enough straight-run can impact a flow meter’s accuracy, immediately reporting inaccurate flow data and impacting a ship’s compliance with ballast water regulations.
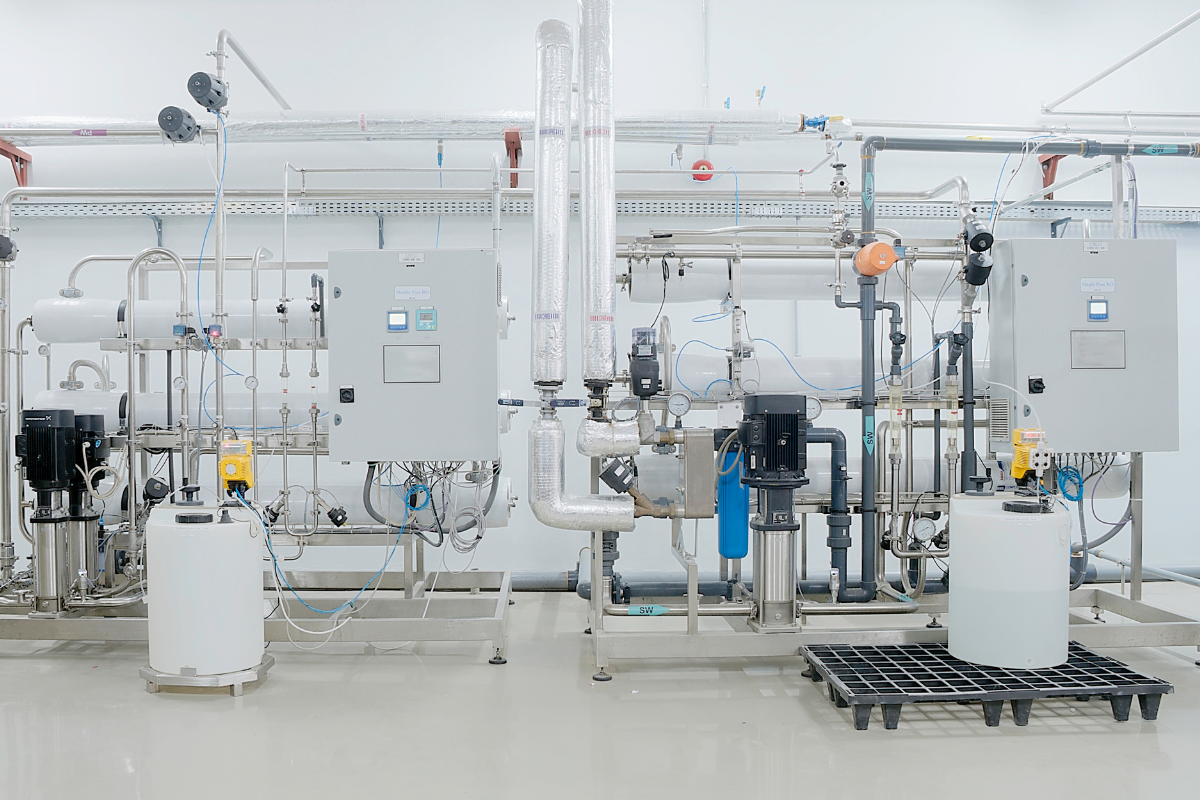
Water treatment processes for ballast water.
Often, the ship’s design, the size of the ballast tanks, and layout of the water treatment system can challenge operators and technicians to find an appropriate flow measurement device. For retrofit projects, the process of identifying the ideal metering location within the existing pipeline can prove difficult, especially if that location requires piping modification.
There are two flow meter technologies often chosen for ballast water flow measurement, including ultrasonic, Coriolis meters, and electromagnetic (mag) meters.
- Ultrasonic Flow Meters. Clamp-on ultrasonic meters are non-intrusive and clamp onto the outside of the pipe rather than installing within the line. This is an attractive option for users wanting to avoid construction costs and time commitments. However, there are potential downfalls to consider. Ultrasonics are sensitive to changes in fluid temperature and salinity, which can affect their accuracy. Changes in fluid properties can lead to errors in flow rate measurements, affecting a ship’s regulatory compliance. Additionally, Ultrasonics may not be as accurate at low flow rates, which can be an issue when ships are taking on or discharging small amounts of ballast water. They’re also susceptible to the buildup of algae or sediment as well, affecting accuracy. Finally, and in many cases most significantly, clamp-on ultrasonic meter technology requires significant straight-run pipe diameters which can be difficult to accommodate in the tight piping requirements onboard a ship.
- Electromagnetic Flow Meters. Mag meters use a magnetic field to measure the flow rate of conductive fluids like seawater. They’re incredibly accurate and suitable for larger ships due to their short straight-run requirements. However, some mag meters may be susceptible to fouling or buildup of sediment, algae, or debris on the sensors, affecting the accuracy and requiring more frequent maintenance. Additionally, some mag meters may not be as accurate at low flow rates, becoming an issue when a ship is taking on or discharging small amounts of ballast water.
Overall, while these meters are all a popular choice for ballast water flow measurement, they both have some limitations to take into consideration when selecting a flow meter for a particular ship or application.
Challenge #3: System Integration
When selecting a flow meter for ballast water applications, it is important to consider factors such as accuracy, reliability, and compatibility with the ship’s existing systems. In addition, the flow meter should be capable of measuring flow rates over a wide range of temperatures, salinities, and flow rates, as these factors can vary depending on the location and time of year.
System integration is a critical aspect of ballast water management, as it ensures that all components of the system are working together seamlessly to meet regulatory requirements and protect the environment. This includes integrating flow meters with components such as pumps, valves, and monitoring systems, as well as with the ship’s control systems and data management software.
By selecting the right flow meter and integrating it seamlessly with other system components, ship operators can ensure that their ballast water management systems are effective, reliable, and efficient. Flow meters with sophisticated output options offer a variety of communication protocols, such as ModBus, Hart, 4-20mA, Ethernet/IP, and more, allowing for reliable flow data to stream into the overarching management software. While the accuracy, meter technology, and other specifications are important to factor into a ship’s ballast water application, the meter is only as useful as its electronics that transmit that data for recording and analysis.
Overall, the most popular system integrations and communication protocols for flow meters in ballast water applications depend on the specific needs and requirements of the ship and their ballast water management system. It’s important to consult with flow meter manufacturers and system integrators to determine the best option for each unique application.
McCrometer’s Recommended Meters for Ballast Water Flow Measurement
Fortunately, the downfalls of electromagnetic flow meters in ballast water applications decrease in McCrometer’s mag meter design. In other mag meters, seawater can be highly corrosive to the electrodes and other components, leading to degradation and failure over time. McCrometer’s full-bore mag meters, such as the Ultra Mag®, are manufactured with the NSF-approved UltraLiner™, a fusion-bonded epoxy that combats corrosion and deterioration from sand, algae, organic particulates, seawater, and more. Unlike other mag meters on the market, the UltraLiner will not delaminate or tear, exposing the meter’s interior components and rendering the meter defunct.
The Ultra Mag also requires 1 diameter upstream and 0 diameters downstream of most flow disturbers, and still maintains up to ±0.5% accuracy (up to ±0.2% with extra calibration) a major benefit for tight spaces and retrofit projects wanting to avoid modifying the existing pipeline setup.
Additionally, McCrometer’s FPI Mag® offers a hot-tap solution for difficult installations and retrofits, requiring minimal-to-no straight-run piping to maintain its reliable ±0.5% accuracy. With no moving parts to repair, the FPI Mag’s multi-electrode water flow sensor contains nothing to wear or break and is generally immune to clogging by sand, grit, or other debris. For large ballast water lines, the FPI Mag is the ideal choice, as the meter is manufactured in sizes 4 to 138” (0.1 m/s – 10 m/s) which makes it an economical solution but also a simpler solution from a logistical installation standpoint.
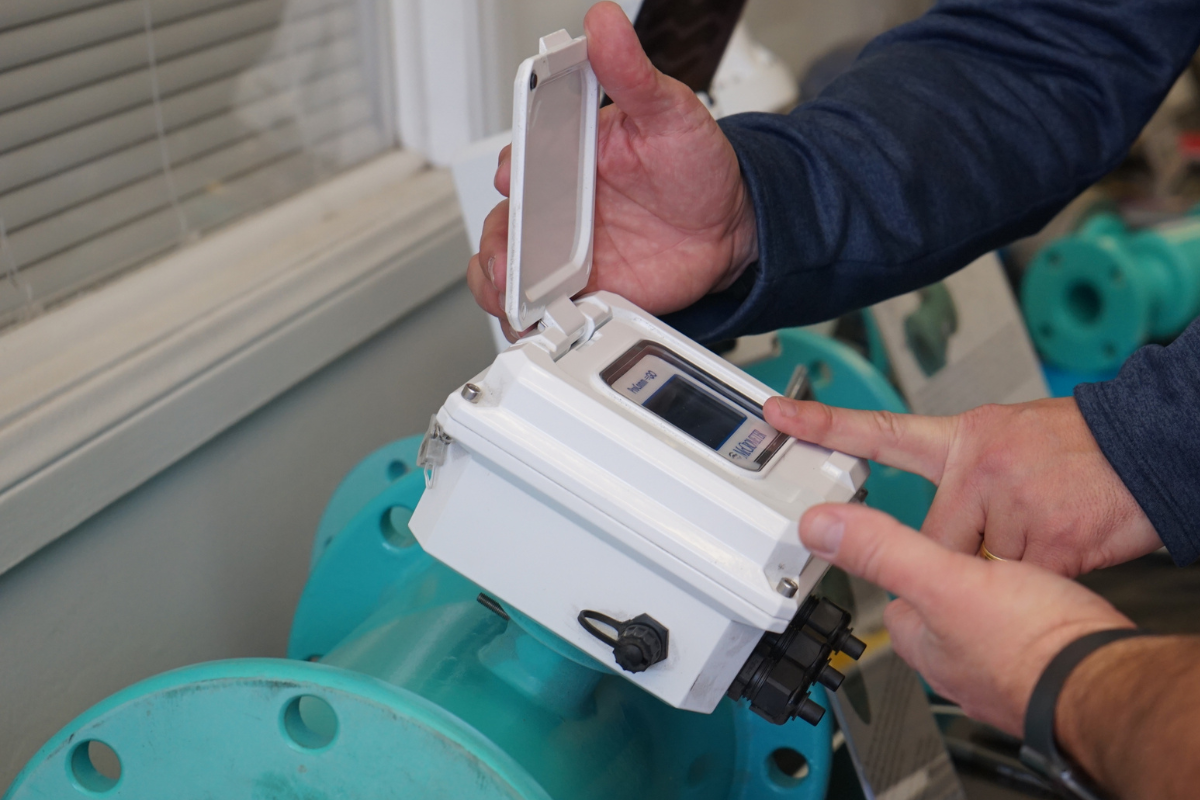
An Ultra Mag with ProComm Go™ converter.
The Ultra Mag and FPI Mag have standard stainless-steel electrodes as a standard, but also offer Hastelloy as a custom option, an ideal choice for seawater measurement. Both meters are accompanied by the ProComm Go™ or ProComm™ electronics, offering battery power or AC/DC power, and a variety of sophisticated output options to seamlessly integrate with ballast water management systems.
For more information about McCrometer’s electromagnetic flow meter suite of products, visit www.mccrometer.com/electromagnetic-flow-meters-family-page
Related Posts
Featured Posts
3 Reasons Why Budget-Focused Farmers Invest in Integrated Telemetry
Allocating budget to flow technology may seem unjustifiable when funds are tight; flow meters and their electronics may already be installed, giving no reason to replace or add additional units when the current solution is in fine working condition. However, flow...
Small Package, Big Impact: The Importance of Desiccant Cartridge Maintenance
You’ve likely seen a desiccant cartridge, in the form of the small silica gel packet accompanying food products, or the activated carbon packet at the top of pharmaceutical bottles. It’s also commonly used in electronics and near sensors, especially for...
Choosing the Right Non-Contact Flow Meters: A Quick Dive into Radar and Laser Technologies
When measuring open channel flow wastewater and stormwater, non-contact flow technology is the ideal method, able to provide an accurate velocity and flow rate. Especially in the wet weather season, non-contact flow technology greatly benefits open channel...
Request More Information